All About Thrust Washers: An Essential Guide for Engineers and Mechanics
Introduction
Thrust washers are critical components in various mechanical systems, serving as barriers between rotating and stationary surfaces to reduce friction and prevent excessive wear. This comprehensive guide delves into the world of thrust washers, exploring their types, materials, applications, design considerations, installation techniques, and more. By understanding the intricacies of thrust washers, engineers and mechanics can optimize system performance, minimize downtime, and extend equipment lifespan.
Types of Thrust Washers
Thrust washers come in a range of types, each designed for specific applications and loads:
-
Flat Washers: The most common type, used in low-load applications where space is limited.
-
Collar Thrust Washers: Feature a flanged collar that aids in alignment and prevents axial movement.
-
Spherical Thrust Washers: Compensate for misalignments and accommodate angular motion.
-
Tapered Thrust Washers: Designed for high thrust loads and provide a wedge-shaped contact surface.
-
Hydrodynamic Thrust Washers: Utilize a film of lubricant to create a lubricating wedge that supports the load.
Materials for Thrust Washers
The choice of material for thrust washers depends on the operating conditions, load requirements, and lubrication:
-
Steel: Durable and commonly used in low to medium-load applications.
-
Bronze: Offers good wear resistance and low friction, suitable for high-speed applications.
-
Babbitt: Soft and conformable, ideal for heavy-load applications where conformability is crucial.
-
Teflon: Resistant to corrosion and chemicals, used in applications with low loads and high temperatures.
-
Ceramic: Extremely hard and wear-resistant, employed in high-load and high-temperature environments.
Benefits of Using Thrust Washers
Thrust washers offer numerous advantages:
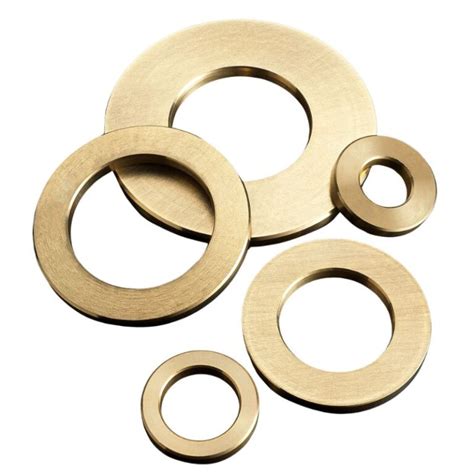
-
Reduced Friction: By providing a barrier between rotating and stationary surfaces, thrust washers significantly reduce friction, minimizing energy loss and wear.
-
Increased Load Capacity: Thrust washers distribute the load over a larger area, allowing for higher load capacities without compromising system integrity.
-
Improved Alignment: Thrust washers help maintain proper alignment between components, preventing misalignment-induced damage.
-
Extended Equipment Life: By reducing friction and wear, thrust washers extend the lifespan of machinery, minimizing downtime and maintenance costs.
Design Considerations for Thrust Washers
Designing effective thrust washers requires careful consideration of the following factors:
-
Load Capacity: Estimate the maximum load the washer will experience to select an appropriate material and thickness.
-
Speed: Consider the rotational speed of the components to ensure the thrust washer can withstand the centrifugal forces.
-
Lubrication: Determine the type and quantity of lubrication required to minimize friction and wear.
-
Temperature: Account for operating temperatures to select a material with suitable thermal stability.
-
Space Constraints: Ensure the thrust washer can fit within the available space while providing adequate load capacity.
Installation of Thrust Washers
Proper installation is essential for optimal performance of thrust washers:

-
Clean Surfaces: Clean the contact surfaces of the mating components to remove any contaminants.
-
Apply Lubricant: Apply an appropriate lubricant to the thrust washer and mating surfaces to reduce friction and wear.
-
Align Components: Carefully align the thrust washer and mating components to ensure proper contact and load distribution.
-
Tighten Securely: Tighten the retaining hardware to the specified torque to secure the thrust washer in place.
Common Mistakes to Avoid with Thrust Washers
To avoid common pitfalls, consider these tips:
-
Overloading: Do not exceed the load capacity of the thrust washer to prevent premature failure.
-
Improper Lubrication: Ensure adequate lubrication is provided to minimize friction and wear.
-
Misalignment: Avoid misalignment between components to prevent uneven load distribution and damage.
-
Incorrect Material Selection: Select the appropriate material based on the operating conditions and load requirements.
-
Insufficient Tolerance: Maintain proper tolerances during manufacturing to ensure the thrust washer fits correctly and functions efficiently.
Applications of Thrust Washers
Thrust washers find applications in a wide range of industries, including:


-
Automotive: In transmissions, differentials, and steering systems to reduce friction and improve performance.
-
Aerospace: In aircraft engines, landing gear, and other critical components to handle high loads and misalignments.
-
Industrial Machinery: In pumps, compressors, and gearboxes to prevent excessive wear and extend equipment lifespan.
-
Renewable Energy: In wind turbines and solar trackers to withstand extreme loads and weather conditions.
-
Medical Equipment: In surgical instruments and prosthetics to provide smooth and precise motion.
Effective Strategies for Thrust Washer Maintenance
Regular maintenance is crucial for ensuring the longevity and effectiveness of thrust washers:
-
Inspect Regularly: Periodically inspect thrust washers for signs of wear, damage, or misalignment.
-
Clean and Lubricate: Clean and lubricate thrust washers as per the manufacturer's recommendations to minimize friction and extend lifespan.
-
Replace When Necessary: Replace worn or damaged thrust washers promptly to prevent system failures and ensure optimal performance.
-
Monitor Temperature: Monitor operating temperatures to identify potential lubrication issues or excessive loads.
-
Keep Records: Maintain accurate records of maintenance and inspection activities for future reference and troubleshooting.
Table 1: Common Thrust Washer Materials and Their Properties
Material |
Characteristics |
Applications |
Steel |
Durable, low cost |
Low to medium loads, general purpose |
Bronze |
Wear-resistant, low friction |
High-speed applications, bearings |
Babbitt |
Soft, conformable |
Heavy loads, high conformability |
Teflon |
Corrosion-resistant, high temperature |
Low loads, chemical resistance |
Ceramic |
Hard, wear-resistant |
High loads, high temperatures |
Table 2: Applications of Thrust Washers in Different Industries
Industry |
Application |
Automotive |
Transmissions, differentials, steering systems |
Aerospace |
Aircraft engines, landing gear |
Industrial Machinery |
Pumps, compressors, gearboxes |
Renewable Energy |
Wind turbines, solar trackers |
Medical Equipment |
Surgical instruments, prosthetics |
Table 3: Tips for Effective Thrust Washer Maintenance
Tip |
Description |
Inspect Regularly |
Check for wear, damage, or misalignment |
Clean and Lubricate |
Minimize friction and extend lifespan |
Replace When Necessary |
Prevent system failures |
Monitor Temperature |
Identify lubrication issues or excessive loads |
Keep Records |
Facilitate troubleshooting and future maintenance |
Call to Action
By understanding the principles of thrust washers and implementing effective design, installation, and maintenance strategies, engineers and mechanics can optimize system performance and extend equipment lifespan. Embrace the benefits of thrust washers today to unlock enhanced efficiency, reliability, and cost savings in your mechanical systems.