Thrust Washers: Ensuring Smooth and Efficient Movement in Mechanical Systems
Thrust washers are essential components in various mechanical systems, playing a crucial role in reducing friction and minimizing wear between rotating or sliding surfaces. These washers are designed to withstand high axial loads and provide precise axial positioning, ensuring smooth and efficient operation of machinery.
Types of Thrust Washers
Thrust washers come in various types, each designed for specific applications:
-
Flat Thrust Washers: The most common type, these washers are flat rings with a uniform thickness. They are suitable for low to moderate loads and speeds.
-
Tapered Thrust Washers: These washers have a tapered surface, allowing them to accommodate misalignment and compensate for angular displacement.
-
Spherical Thrust Washers: Designed to handle high axial and radial loads, these washers have a spherical surface that allows for greater conformity and load distribution.
-
Collar Thrust Washers: These washers are mounted on a shaft or hub, providing a bearing surface for the thrust load.
Materials Used in Thrust Washers
Thrust washers are fabricated from various materials, including:
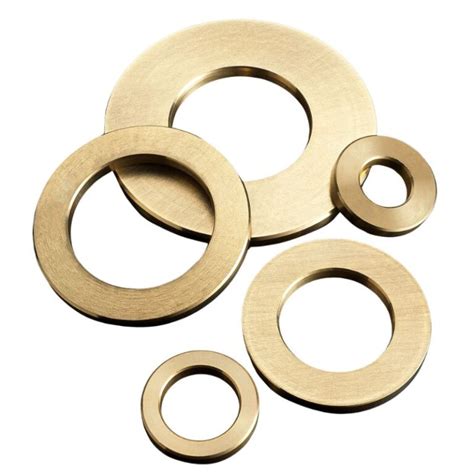
-
Steel: Durable and cost-effective, steel washers are commonly used in general-purpose applications.
-
Bronze: Offers low friction and wear resistance, making it suitable for high-speed applications.
-
Babbitt Metal: A soft alloy that conforms to mating surfaces, providing excellent load-bearing capacity.
-
Nylon: A lightweight and economical material with good wear resistance and vibration damping properties.
-
PTFE: A high-performance plastic that offers low friction, corrosion resistance, and high temperature tolerance.
Benefits of Using Thrust Washers
The use of thrust washers provides several advantages in mechanical systems:
-
Reduced Friction: Thrust washers effectively reduce friction between moving surfaces, minimizing energy losses and heat generation.
-
Increased Bearing Life: By distributing loads evenly, thrust washers reduce wear on mating surfaces, extending the life of bearings and other components.
-
Improved Alignment: Thrust washers help maintain proper alignment between rotating or sliding components, preventing premature wear and failure.
-
Compensation for Misalignment: Tapered and spherical thrust washers can accommodate misalignment and uneven loads, ensuring smooth operation even under adverse conditions.
Applications of Thrust Washers
Thrust washers find application in a wide range of industries, including:
-
Automotive: Transmissions, differentials, and steering systems
-
Aerospace: Engines, gearboxes, and landing gear
-
Industrial Machinery: Pumps, compressors, and conveyors
-
Agricultural Equipment: Tractors, combines, and harvesters
-
Construction Equipment: Excavators, bulldozers, and cranes
Design Considerations for Thrust Washers
When selecting and designing thrust washers, several factors need to be considered:

-
Load Capacity: The washer must be able to withstand the axial loads imposed on it.
-
Speed: The washer must be suitable for the operating speed of the system.
-
Materials: The washer material should be compatible with the mating surfaces and operating environment.
-
Lubrication: The washer may require lubrication to minimize friction and wear.
-
Cost: The cost of the washer should be considered within the project budget.
Tips and Tricks for Using Thrust Washers
-
Proper Lubrication: Ensure that thrust washers are properly lubricated to reduce friction and wear.
-
Surface Finish: Smooth and polished surfaces on thrust washers and mating components minimize friction.
-
Preloading: Preloading thrust washers can increase load capacity and rigidity while reducing noise and vibration.
-
Monitoring: Regularly inspect thrust washers for wear or damage to ensure optimal performance.
Pros and Cons of Thrust Washers
Pros:
- Reduced friction
- Increased bearing life
- Improved alignment
- Compensation for misalignment
- Wide range of applications
Cons:

- Can be expensive
- Require precise manufacturing
- May require lubrication
- Can be susceptible to wear and damage
Common FAQs about Thrust Washers
1. What is the difference between a thrust washer and a bearing?
A thrust washer is designed to handle axial loads, while a bearing supports radial and thrust loads.
2. What are the different types of materials used in thrust washers?
Steel, bronze, babbitt metal, nylon, and PTFE are commonly used materials.

3. How do I select the right thrust washer for my application?
Consider load capacity, speed, materials, and lubrication requirements.
4. How often should I inspect thrust washers?
Regular inspection is recommended to ensure optimal performance and address any issues early on.
5. Can I use thrust washers to compensate for misalignment?
Tapered and spherical thrust washers are designed to accommodate misalignment.
6. What are some common causes of thrust washer failure?
Lack of lubrication, improper alignment, excessive loads, and wear are common causes of failure.
Conclusion
Thrust washers are critical components that ensure smooth and efficient operation in mechanical systems. By understanding the different types, materials, benefits, and design considerations, engineers can select and use thrust washers effectively to optimize performance and longevity in various applications. Proper maintenance and monitoring are crucial to ensure that thrust washers continue to perform optimally, reducing downtime and extending the life of mechanical systems.