Thrust Washers: Essential Components for Rotating Machinery
Thrust washers are vital components in rotating machinery, designed to manage axial forces and prevent excessive wear and damage. They are typically thin, disc-shaped components placed between rotating and stationary surfaces to distribute loads evenly and reduce friction.
Types of Thrust Washers
There are several types of thrust washers, each suited for specific applications:
-
Plain Thrust Washers: Simple, ring-shaped washers made of materials like steel, bronze, or plastic.
-
Laminated Thrust Washers: Consisting of thin layers of alternating materials, providing higher load capacity and noise reduction.
-
Ball Thrust Washers: Utilize ball bearings to carry axial loads, allowing for higher speeds and reduced friction.
-
Tapered Thrust Washers: Designed with a tapered bore, compensating for shaft misalignment and ensuring proper contact.
Materials for Thrust Washers
The material used for thrust washers is crucial and depends on the operating conditions:
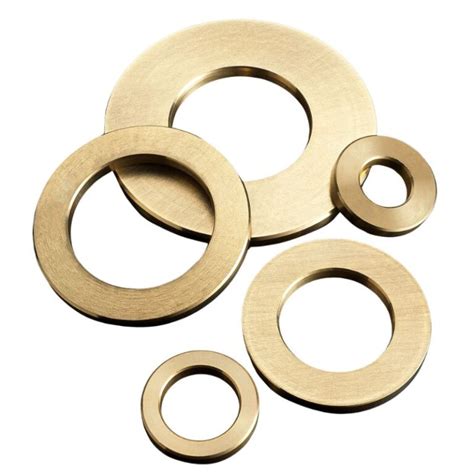
-
Steel: Provides high strength and wear resistance, suitable for heavy-duty applications.
-
Bronze: Offers good wear resistance and corrosion resistance, ideal for marine and chemical environments.
-
Plastic: Lightweight and corrosion-resistant, suitable for low-load and non-lubricated applications.
-
Composite Materials: Combine the properties of different materials, providing specific characteristics like low friction or high thermal conductivity.
Why Thrust Washers Matter
Thrust washers play a critical role in rotating machinery:
-
Distribute Axial Loads: They prevent excessive axial force from damaging bearings or shafts.
-
Reduce Friction: By separating rotating and stationary surfaces, they minimize friction and improve efficiency.
-
Enhance Stability: They stabilize rotating components, preventing axial movement and reducing vibration.
-
Extend Component Life: Proper lubrication and maintenance of thrust washers can significantly increase the lifespan of other machinery components.
Benefits of Using Thrust Washers
-
Improved Efficiency: Reduced friction translates to lower energy consumption and increased operational efficiency.
-
Enhanced Durability: Protected components lead to extended machine life and reduced maintenance costs.
-
Smooth Operation: Reduced vibration and stabilized components minimize noise and improve overall operation.
-
Reduced Downtime: By preventing damage and extending component life, thrust washers reduce the risk of unexpected breakdowns and costly downtime.
Applications of Thrust Washers
Thrust washers find applications in a wide range of industries, including:
-
Automotive: Transmissions, differentials, and other rotating components.
-
Aerospace: Jet engines, turbine engines, and flight control systems.
-
Industrial Machinery: Gearboxes, compressors, and pumps.
-
Oil and Gas: Drill bits, blow-out preventers, and submersible pumps.
-
Medical Devices: Artificial joints, dental equipment, and surgical tools.
Stories to Learn From
-
The Worn Thrust Washer: A worn thrust washer in a gearbox caused excessive axial movement, resulting in premature bearing failure. Timely replacement of the thrust washer prevented further damage and costly downtime.
-
The Misaligned Installation: A misaligned thrust washer in a pump led to uneven loading and accelerated wear. Proper installation and alignment ensured the washer's effectiveness and extended the pump's life.
-
The Lubrication Failure: Lack of lubrication on a thrust washer caused excessive friction and heat buildup, leading to premature failure. Adequate lubrication and maintenance practices are essential for optimal performance.
Frequently Asked Questions (FAQs)
- What is the difference between a plain thrust washer and a ball thrust washer?
A plain thrust washer uses a solid material, while a ball thrust washer employs ball bearings to carry axial loads. Ball thrust washers offer higher load capacity and reduced friction.

- How do I choose the right material for a thrust washer?
Consider the operating conditions, such as load, speed, temperature, and lubrication availability. Steel is a good choice for high loads, while bronze provides corrosion resistance.
- How often should thrust washers be replaced?
Replacement frequency varies based on the application, but regular inspection and maintenance are crucial. Premature wear or damage are signs of potential replacement needs.

- Can thrust washers be used in high-speed applications?
Yes, ball thrust washers are specifically designed for high-speed applications due to their reduced friction and ability to handle high loads.

- What are the key factors to consider when specifying a thrust washer?
Load capacity, speed, operating conditions, and lubrication availability are essential factors to consider for optimal selection.
- How do I prevent thrust washer failures?
Proper lubrication, correct installation, alignment, and regular maintenance are crucial for preventing failures and extending thrust washer lifespan.
Call to Action
Thrust washers are essential components for rotating machinery, ensuring efficient and reliable operation. By understanding their types, materials, applications, and benefits, you can make informed decisions about specifying and maintaining thrust washers. Remember, the proper selection and maintenance of thrust washers can significantly improve the performance and longevity of your equipment.