The Ultimate Guide to Replacement Bearings: Ensuring Optimal Performance and Longevity
Introduction
Replacement bearings play a crucial role in maintaining the smooth operation, efficiency, and longevity of various industrial equipment, vehicles, and machinery. They are essential components that reduce friction, minimize wear, and allow moving parts to rotate seamlessly. This comprehensive guide will delve into the significance of replacement bearings, exploring their types, applications, benefits, and effective maintenance strategies.
Types of Replacement Bearings
The diverse range of industrial applications demands a variety of bearing types. Some of the most common include:
-
Ball bearings: The most widely used type, they consist of rows of hardened steel balls rolling between inner and outer rings.
-
Roller bearings: Utilize cylindrical or tapered rollers that provide higher load capacity and resistance to shock loads.
-
Needle bearings: Featuring thin, needle-shaped rollers, they offer a compact design and high load-carrying capacity.
-
Thrust bearings: Designed to handle axial loads, they prevent axial movement while allowing radial motion.
-
Linear bearings: Enable precise linear motion in applications where rotational movement is impractical.
Applications of Replacement Bearings
Replacement bearings find application in countless industries and sectors, including:

-
Automotive: Transmissions, wheel hubs, and steering systems
-
Industrial machinery: Conveyors, pumps, and machine tools
-
Aerospace: Engines, landing gear, and flight control systems
-
Medical equipment: Surgical tools, imaging devices, and patient care equipment
-
Consumer appliances: Washing machines, dryers, and refrigerators
Why Replacement Bearings Matter
The importance of replacement bearings cannot be overstated. They:
-
Reduce friction: Bearings minimize the resistance between moving parts, reducing energy consumption and wear.
-
Enhance performance: Proper bearing lubrication ensures smooth operation and maintains optimal efficiency.
-
Extend equipment life: Well-maintained bearings prevent premature failure of machinery, reducing downtime and maintenance costs.
-
Improve safety: Bearings are critical safety components, reducing accidents caused by equipment malfunctions.
Benefits of Replacing Bearings
Replacing worn or damaged bearings offers numerous benefits:
-
Increased productivity: Smooth operation and reduced friction lead to higher output and efficiency.
-
Reduced maintenance costs: Proactive bearing replacement prevents costly breakdowns and repairs.
-
Extended equipment life: Replacing bearings before failure extends the lifespan of machinery and reduces replacement costs.
-
Improved safety: Reliable bearings minimize the risk of accidents and ensure the safe operation of equipment.
Effective Bearing Maintenance Strategies
Proper maintenance is essential for maximizing bearing performance and longevity. Here are effective strategies:
-
Regular inspections: Regularly inspect bearings for signs of wear, damage, or contamination.
-
Proper lubrication: Follow manufacturer's recommendations for lubrication type, frequency, and quantity.
-
Condition monitoring: Utilize vibration analysis or other monitoring techniques to detect bearing issues early.
-
Avoid overloading: Ensure that bearings are not subjected to excessive loads that could cause premature failure.
-
Proper storage: Store bearings in a clean, dry environment to prevent corrosion and damage.
Tips and Tricks
-
Use high-quality bearings: Opt for bearings from reputable manufacturers to ensure durability and reliability.
-
Consider bearing load capacity: Choose bearings that can withstand the specific loads and speeds of the application.
-
Lubricate sparingly: Over-lubrication can attract dirt and contaminants that can accelerate bearing wear.
-
Monitor bearing temperature: High operating temperatures indicate potential bearing problems that require attention.
-
Seek professional assistance: Consult with a bearing specialist for proper bearing selection and maintenance advice.
Humorous Stories About Replacement Bearings
Story 1:
A mechanic was working on a car when he heard a strange noise. Puzzled, he called his supervisor over, who listened intently. "That sounds like a bad bearing," the supervisor said. The mechanic nodded in agreement and replied, "Yeah, I thought it was a squeak, but it's actually a growler!"
Lesson: Even the most experienced mechanics can be fooled by bearing noises.
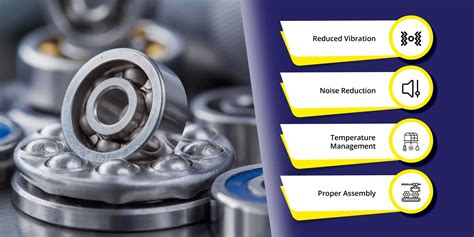
Story 2:
A homeowner was trying to fix a noisy washing machine. He removed the bearing and noticed that it was completely dry. "No wonder it's making noise," he muttered to himself. "It's a thirsty bearing!"

Lesson: Lubricating bearings regularly is essential to prevent wear and noise.
Story 3:
A pilot was landing a plane when the landing gear failed. The plane crashed into a field, but fortunately, the pilot survived. When asked how he felt, he replied, "I'm okay, but I think the bearings on my plane aren't doing so well."
Lesson: Bearings are critical components for the safe and reliable operation of machinery.
Comparative Tables
Bearing Type |
Advantages |
Disadvantages |
Ball bearings |
High speed |
Lower load capacity |
Roller bearings |
High load capacity |
Higher friction |
Needle bearings |
Compact design |
Sensitive to misalignment |
Thrust bearings |
Handle axial loads |
Limited speed |
Causes of Bearing Failure |
Percentage |
Wear |
80% |
Contamination |
10% |
Overloading |
5% |
Misalignment |
3% |
Corrosion |
2% |
Signs of Bearing Wear |
Description |
Increased noise |
Grating, squeaking, or rumbling sounds |
Increased vibration |
Excessive movement or shaking |
Heat generation |
Warm or hot bearings |
Reduced efficiency |
Machinery operates sluggishly or with increased energy consumption |
Excessive play |
Loose or wobbly movement in the bearing |
Frequently Asked Questions (FAQs)
-
How often should I replace bearings?
It depends on the application and operating conditions. Consult with a bearing specialist or refer to manufacturer's recommendations.
-
Can I replace bearings myself?
It is possible, but it requires specialized knowledge and tools. Consider seeking professional assistance for complex or critical applications.
-
How much does it cost to replace bearings?
The cost varies depending on the bearing type, size, and application. Get quotes from multiple vendors to find the most competitive price.
-
What are the signs of a failed bearing?
Excessive noise, vibration, heat, reduced efficiency, and increased play.
-
Can I prevent premature bearing failure?
Yes, by following proper maintenance practices, using high-quality bearings, and avoiding overloading.
-
What is the best type of bearing lubricant?
The appropriate lubricant depends on the bearing type and application. Consult with a bearing specialist or refer to manufacturer's recommendations.
-
How do I know if a bearing is misaligned?
Excessive vibration, increased noise, and premature bearing failure can indicate misalignment.
-
Why is it important to use high-quality bearings?
High-quality bearings are manufactured with precision and durability, ensuring optimal performance and extended lifespan.
Conclusion
Replacement bearings are indispensable components that play a vital role in the smooth and efficient operation of countless industrial and consumer applications. By understanding the types, benefits, and maintenance strategies associated with replacement bearings, businesses and individuals can maximize the performance, longevity, and safety of their machinery and equipment. Remember, proactive bearing maintenance and timely replacement prevent costly breakdowns, reduce downtime, and ensure the reliable performance of your machinery for years to come.