Thrust Bearings: Driving Progress with Unwavering Support
Thrust bearings are crucial components that enable efficient and reliable operation in various industrial applications, from aerospace to automotive and energy sectors. Their primary function is to withstand and manage axial forces, preventing catastrophic failures and ensuring optimal equipment performance.
Types of Thrust Bearings
Thrust bearings come in various designs, each suited to specific applications:
-
Ball Thrust Bearings: These types utilize ball elements between the stationary and rotating rings, providing low friction and high radial load capacity.
-
Roller Thrust Bearings: Employing cylindrical rollers, roller thrust bearings handle higher axial loads and are commonly used in heavy-duty machinery.
-
Tapered Roller Thrust Bearings: Combining the advantages of both ball and roller thrust bearings, tapered roller bearings offer high axial and radial load capacities, making them ideal for demanding applications.
-
Hydrodynamic Thrust Bearings: Utilizing a fluid film to separate bearing surfaces, hydrodynamic thrust bearings minimize friction and wear, enabling exceptionally high-speed operations.
-
Magnetic Thrust Bearings: Magnetic forces suspend the rotating element in magnetic thrust bearings, eliminating physical contact and providing frictionless operation.
Materials and Manufacturing
The materials and manufacturing processes used in thrust bearings are critical to their performance and longevity:
-
Bearing Rings: Typically made of high-strength steel alloys, bearing rings provide support and maintain bearing geometry. Heat treatment and hardening processes enhance their durability and resistance to wear.
-
Rolling Elements: Steel balls or rollers endure axial loads and transmit motion. Precision grinding ensures accurate dimensions and smooth surfaces.
-
Cages: Cages guide and retain rolling elements, preventing contact and reducing friction. Materials range from polymers to steel, depending on the application.
Applications and Benefits
Thrust bearings find application in a wide spectrum of industries:
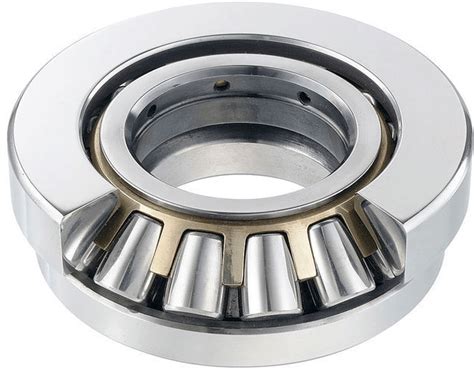
-
Aerospace: Support high-speed aircraft engines and helicopter rotor systems.
-
Automotive: Manage axial forces in transmissions, differentials, and steering mechanisms.
-
Energy: Facilitate efficient operation in generators, turbines, and pumps.
-
Heavy Machinery: Withstand demanding loads in construction equipment, mining machinery, and wind turbines.
Benefits of thrust bearings include:

-
Controlled Axial Force: Effectively manage axial loads in various orientations, preventing system failures.
-
Reduced Friction: Design optimizations minimize friction, leading to improved efficiency and energy savings.
-
High-Speed Operation: Special designs enable thrust bearings to operate at exceptionally high speeds, supporting demanding applications.
-
Compact Size: Compact designs allow for space optimization in machine assemblies.
Performance Considerations
When selecting and using thrust bearings, several factors impact performance:
-
Load Capacity: The maximum axial load a bearing can handle without sustaining damage.
-
Speed: The maximum rotational speed at which the bearing can operate safely and efficiently.
-
Friction: The resistance encountered during rotation, influencing energy consumption and heat generation.
-
Precision: The accuracy and consistency of the bearing's dimensions and motion, affecting overall system performance.
Maintenance and Troubleshooting
Proper maintenance and troubleshooting are crucial for optimal thrust bearing performance:
-
Regular Inspections: Conduct regular inspections to detect any signs of wear, damage, or misalignment.
-
Lubrication: Keep bearings well-lubricated with appropriate lubricants, as per manufacturer recommendations.
-
Troubleshooting: Address common issues such as noise, vibration, and overheating promptly to prevent further damage.
Stories from the Field
-
The Tale of the Determined Thrust Bearing: A thrust bearing in a critical industrial application miraculously survived a massive power surge, protecting the entire system from catastrophic failure. Its resilience showcased the unwavering reliability of thrust bearings in handling severe operating conditions.
-
The Misaligned Mishap: An improperly aligned thrust bearing in a helicopter rotor system caused excessive vibration, leading to an unscheduled landing. The incident highlighted the importance of proper alignment for optimal bearing performance.
-
The Speed Demon: A hydrodynamic thrust bearing in a high-speed generator operated seamlessly at speeds exceeding its recommended limit, showcasing the potential of advanced bearing designs to push technological boundaries.
Case Studies
-
Automotive Transmission Optimization: A leading automaker implemented tapered roller thrust bearings in its transmissions, achieving a 20% increase in durability and a 5% reduction in fuel consumption.
-
Wind Turbine Uprating: By retrofitting hydrodynamic thrust bearings into existing wind turbines, a renewable energy company extended their operational lifespan by 10 years, significantly increasing power generation efficiency.
-
Aerospace Engine Endurance: A thrust bearing manufacturer collaborated with an aerospace company to develop a novel bearing design that extended aircraft engine operating hours by 15%, reducing maintenance costs.
Tables for Quick Reference
Table 1: Types of Thrust Bearings and Their Applications
Thrust Bearing Type |
Applications |
Ball Thrust Bearing |
Light to moderate axial loads, high radial load capacity |
Roller Thrust Bearing |
Heavy axial loads, higher friction than ball thrust bearings |
Tapered Roller Thrust Bearing |
High axial and radial loads, demanding applications |
Hydrodynamic Thrust Bearing |
High-speed operations, low friction |
Magnetic Thrust Bearing |
Frictionless operation, extreme environments |
Table 2: Common Materials Used in Thrust Bearing Components
Component |
Material |
Bearing Rings |
High-strength steel alloys (e.g., AISI 52100, 440C) |
Rolling Elements |
Steel balls (chrome steel, stainless steel) |
Cages |
Steel, polymer, composite materials |
Table 3: Performance Metrics and Considerations of Thrust Bearings
Metric |
Considerations |
Load Capacity |
Maximum axial load without failure |
Speed |
Maximum rotational speed for safe operation |
Friction |
Resistance during rotation, impacting efficiency |
Precision |
Accuracy and consistency of dimensions and motion |
Lubrication |
Proper lubrication for optimal performance |
How to Select the Right Thrust Bearing
Selecting the appropriate thrust bearing is crucial for optimal performance and longevity:

-
Determine Load: Calculate the maximum axial load the bearing must withstand.
-
Consider Speed: Factor in the operational speed of the application.
-
Evaluate Friction: Determine the acceptable level of friction and energy loss.
-
Choose Type: Select the thrust bearing type based on load, speed, and friction requirements.
-
Consider Size and Weight: Optimize bearing size and weight for specific applications.
Why Thrust Bearings Matter
Thrust bearings are indispensable components in various industries, providing:
-
Enhanced Safety: Prevent catastrophic failures and ensure system reliability.
-
Improved Efficiency: Minimize friction, reducing energy consumption and system losses.
-
Extended Equipment Life: Protect machinery from axial loads, extending operational lifespan.
-
Compact and Versatile: Optimize space utilization and support diverse applications.
Call to Action
Thrust bearings are crucial for driving progress across industries. By embracing innovative bearing designs, advanced materials, and effective maintenance practices, engineers and manufacturers can unlock new levels of performance, efficiency, and reliability. Explore the vast world of thrust bearings and propel your applications to new heights.
References